
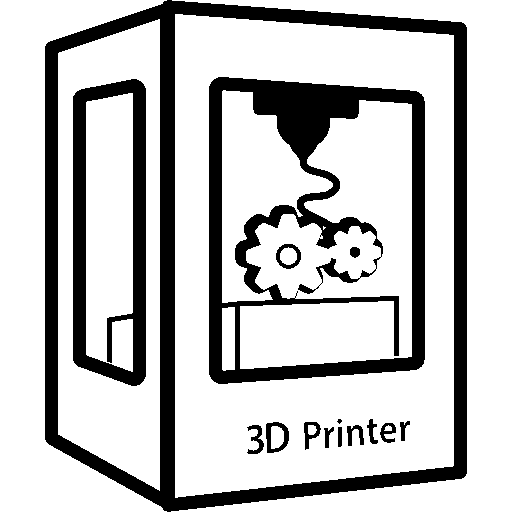
My quick and dirty math based on some captions of the figures from the paper suggest it’s unlikely they’re getting amplification for now, because it seems like the even the “low” resistance state is quite resistive. But I still suspect it can be done, and they do characterize their structures as “active” - thanks!
Unless I’m reading this too optimistically, it seems like recovering the resin just requires adding more of the original solvent, which sounds pretty good (as long as that solvent isn’t much nastier than a regular resin solvent).